Elan Yachts: Innovative Hull Construction with Composite Technology
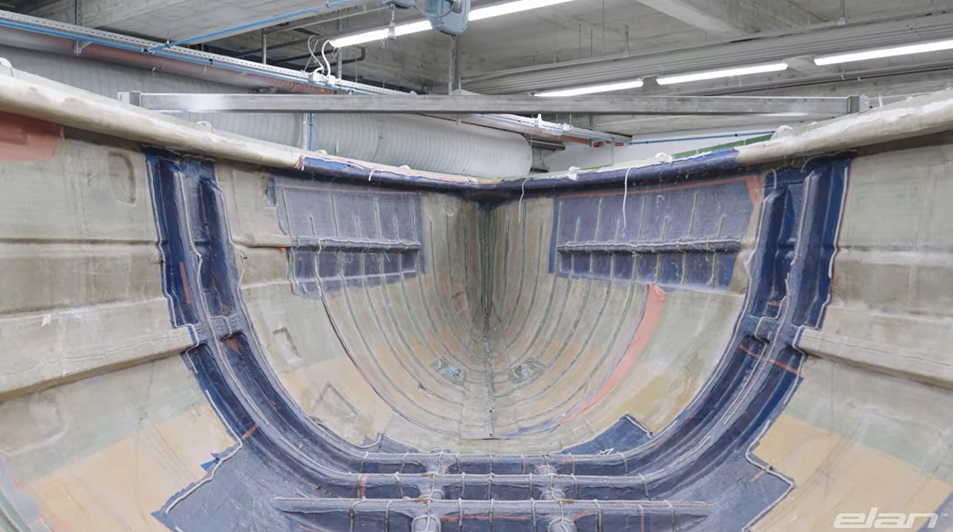
Discover Elan Yachts' innovative composite technology
Today we dive into the advanced composite knowledge and techniques that Elan Yachts uses to build their yachts. From a rich history to innovative manufacturing processes like VAIL, discover how Elan stands out in the world of yacht building.
A Rich History of Composite Work
Elan's Early Years
This year Elan Yachts celebrates its 75th anniversary. In the 1960s, Elan produced its first fiberglass reinforced plastic (GRP) products, including skis, canoes and small boats.
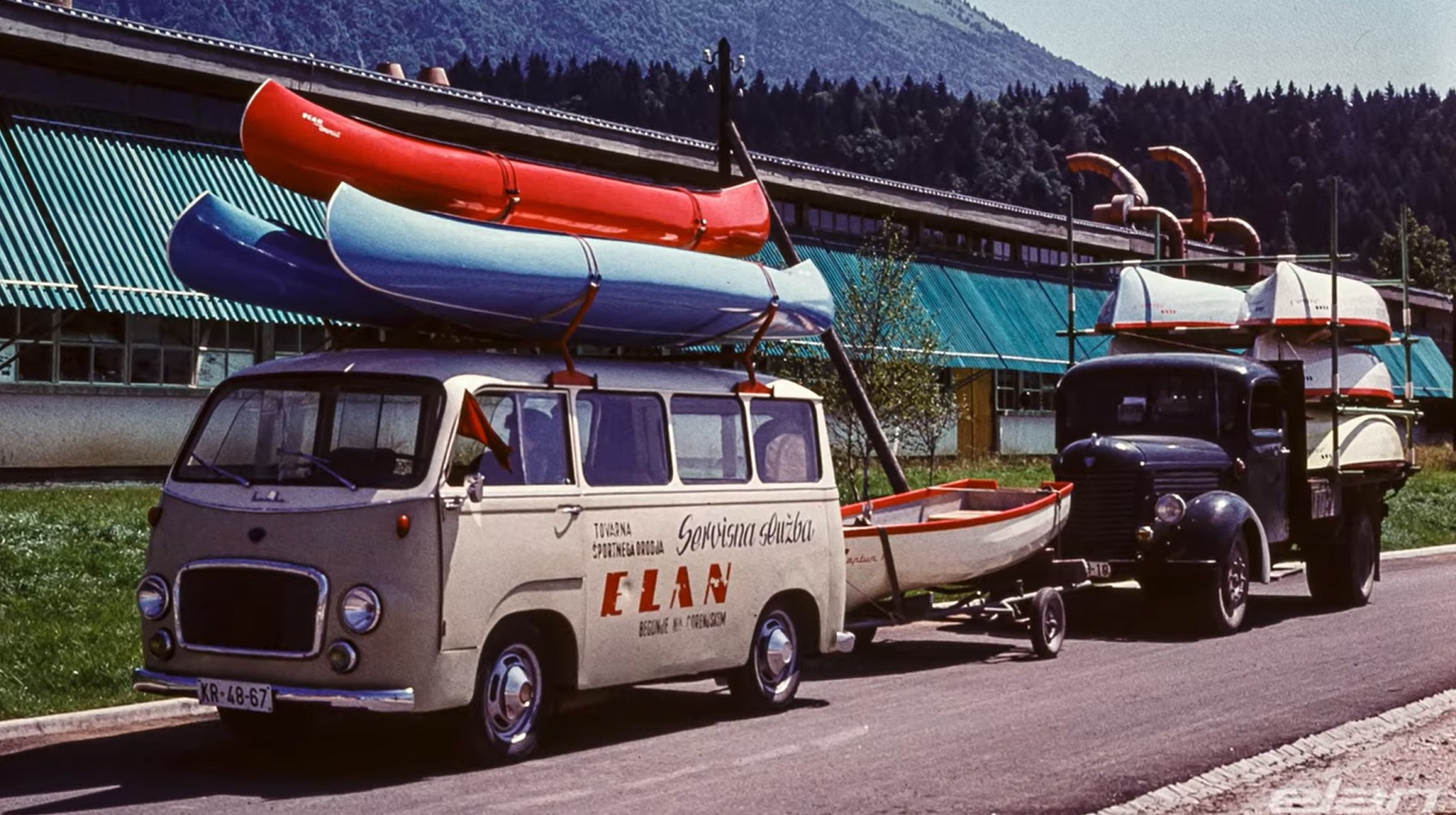
Expansion into Composite Work
Shortly thereafter, Elan established a specialized composite workshop that manufactured a variety of products, from automotive parts to sports equipment. With growing demand, the company eventually focused on skis and yachts.
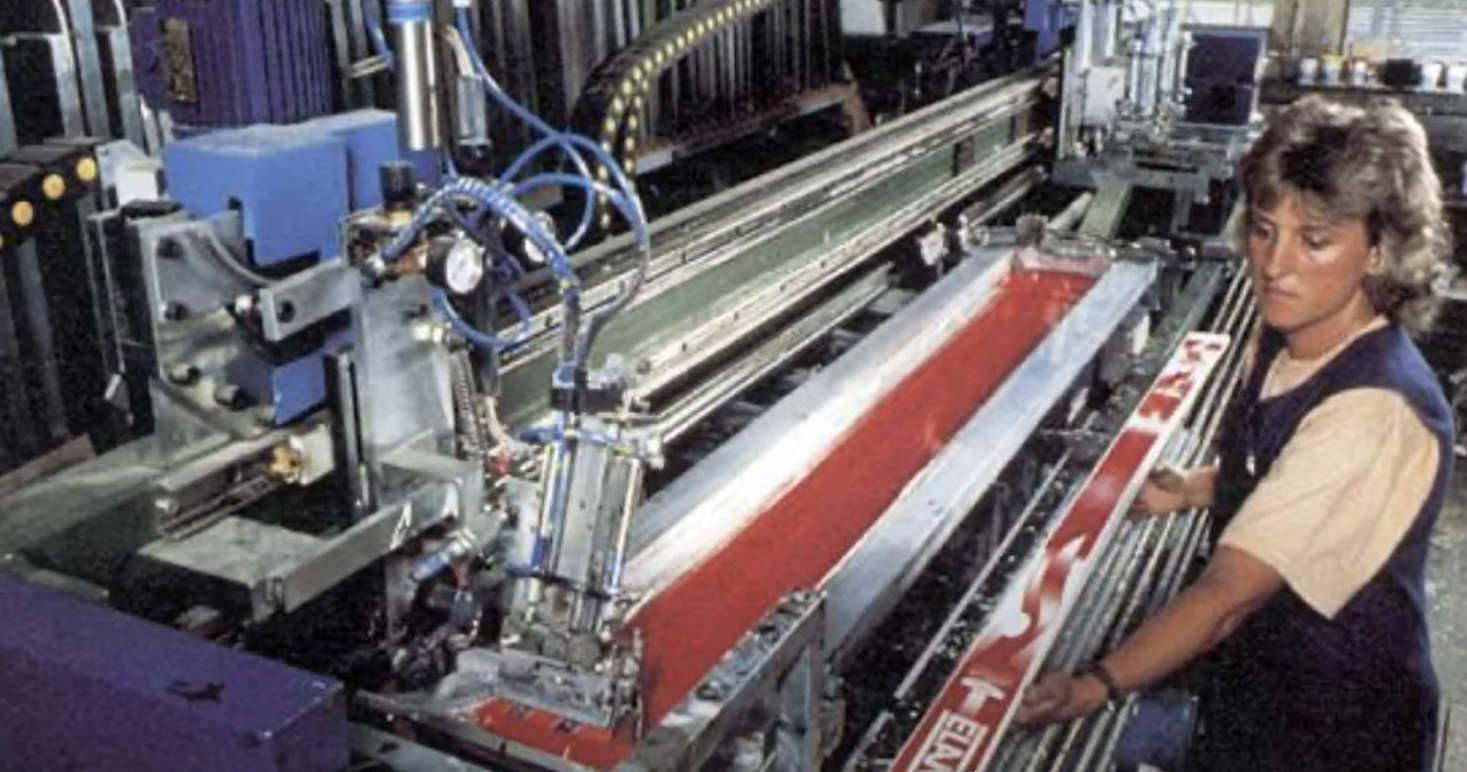
Innovation with VAIL technology
In 2003, Elan was one of the first European yacht builders to adopt Vacuum Assisted Infusion Lamination (VAIL) technology. This high-tech method set new standards in yacht production.
What is VAIL?
VAIL is a modern process in which resin is evenly dispersed through glass fibers using a vacuum pump. This eliminates air pockets, reduces material usage and ensures a consistent final product.
Osmosis protection with Front Laminate
Before the actual infusion, Elan applies a protective pre-laminate. This layer, made of gelcoat and vinylester resin, forms a barrier against osmosis and guarantees a smooth surface.
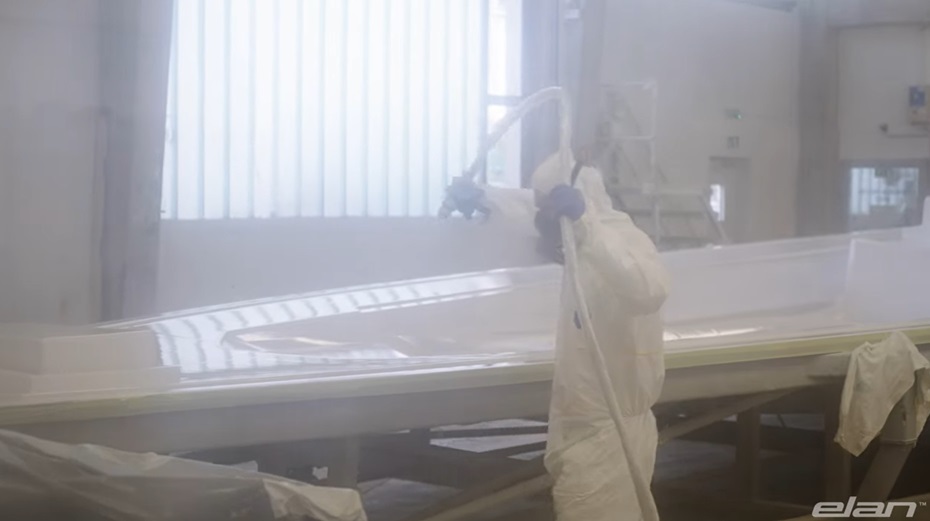
Elan was one of the first shipyards to adopt vacuum assisted infusion lamination technology in 2003 , setting a precedent as the first European manufacturer of series yachts to adopt this technique. The expertise of composite in yacht building even led to the creation of a dedicated composite department, which now produces complex composite parts for various industries, such as the aerospace, automotive and wind industries.
VAIL lamination How Does This Process Work?
VAIL, or Vacuum Assisted Infusion Lamination, is an advanced and efficient technique for laminating composites. It replaces traditional methods and offers significant advantages in terms of quality, efficiency and environmental friendliness.
Traditional Lamination
In traditional lamination, fiberglass is manually saturated with resin. This process includes:
- Manual application of resin to fiberglass layers.
- Using a roller to remove air and ensure complete saturation.
- Waiting for the laminate to cure.
Although effective, this method has limitations, such as the risk of air entrapment and uneven distribution of resin.
How Does VAIL Work?

VAIL technology takes lamination to the next level using vacuum technology and computer-controlled precision. The process works as follows:
- Fiberglass Lay-up:
A predetermined fiberglass plan is carefully placed on a mold. This plan is designed using advanced computer modeling to ensure optimal strength and performance. - Installation of Distribution Tubes:
A network of perforated distribution tubes is strategically laid across the mold. - Airtight Sealing:
The mold is covered with an airtight plastic film to completely seal the system. - Vacuum and Infusion:
- One end of the pipe system is connected to a resin container.
- The other end is connected to a powerful vacuum pump.
- The vacuum pump pulls resin through the distribution tubes, evenly saturating the glass fibers.
- Curing:
The laminate is cured evenly, resulting in a strong, light and consistent finished product.
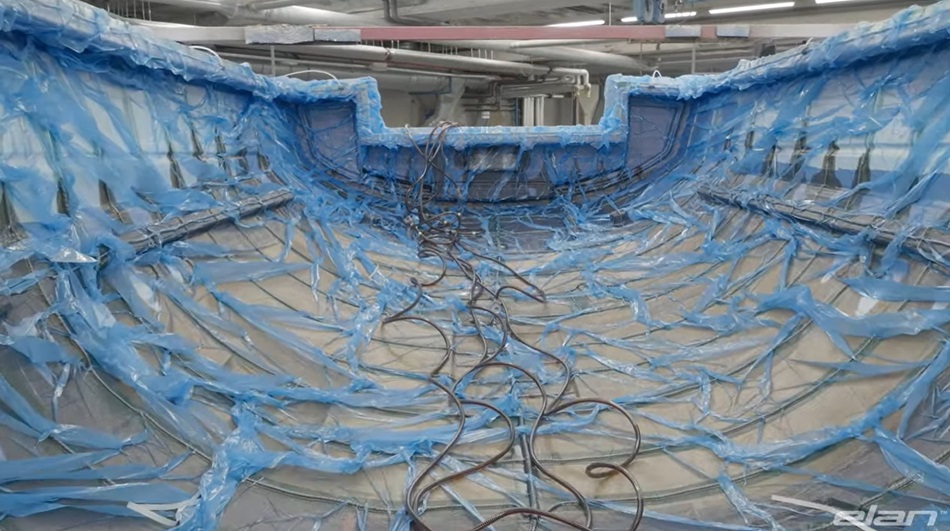
Benefits of VAIL
- Full Saturation: No air inclusions, minimizing the possibility of delamination.
- Efficiency: Only the exact amount of resin is used, reducing material waste.
- Consistency: Mechanical properties remain uniform, making each product of high quality.
- Environmentally friendly: Reduced resin fumes and a healthier working environment for factory workers.
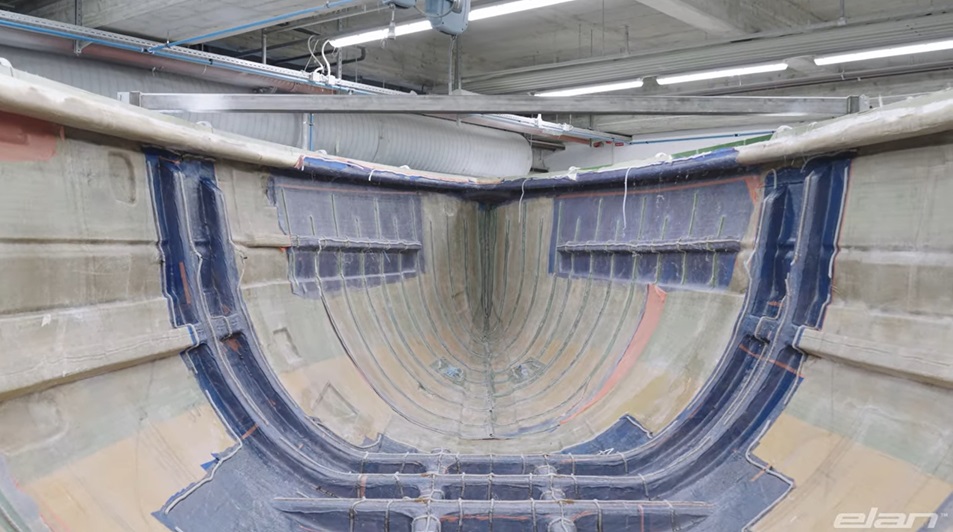
Applications in Other Industries
Elan's expertise in composites goes beyond yacht building. Its dedicated composites department produces parts for the aerospace, automotive and wind industries.
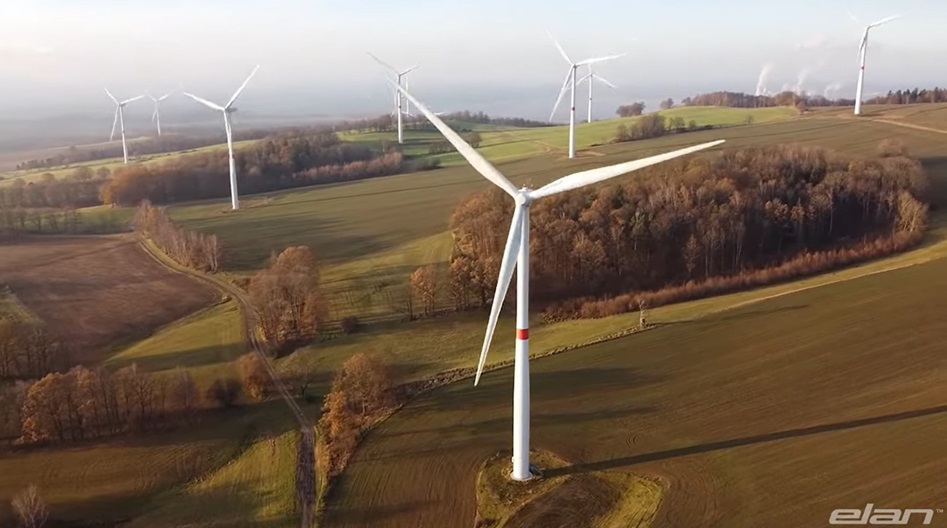
View the VAIL process in Action
Wondering how the VAIL process works? Watch our video where we take you step by step through this innovative production process.
.webp)